Steel - Kirloskar Ferrous
Carbon, Alloy and Bearing Steel for Various Industries Application.
ISMT is an established market leader in the production of special engineering steels. We produce carbon, alloy and martensitic stainless steel bars with a special emphasis on ultra-clean steels, free machining steels, bearing steels, and on other specially engineered steel grades. With over 15 years of experience in the manufacture of special steels our strength lies in our ability to produce very clean steels consistently and cost effectively; to produce hard to manufacture free machining steels; to develop and custom produce steels that meet specific mechanical or metallurgical requirements; and to deliver small lots of steels.
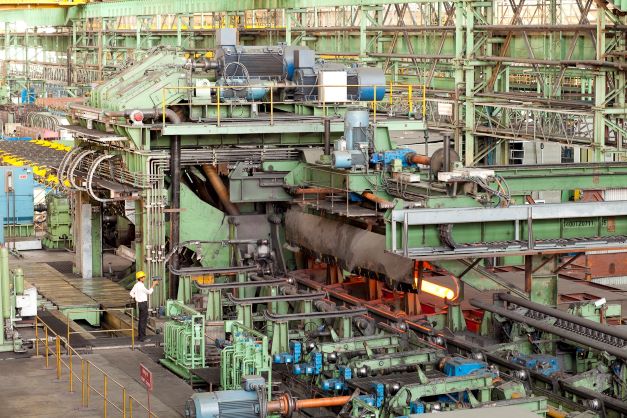
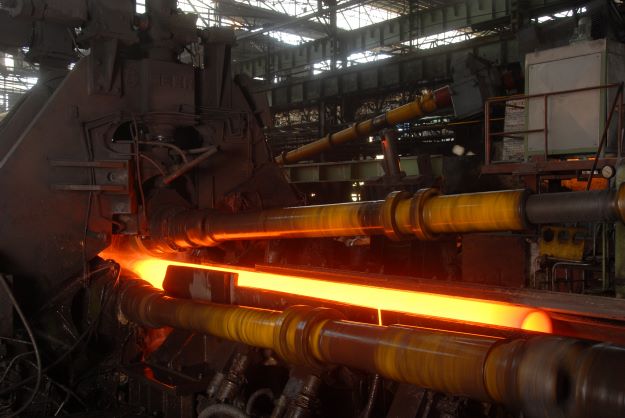
Modern Equipment and Methods
We operate one of the most modern alloy steel plants in the country located at Jejuri, near Pune. All our steel is produced through the electric arc furnace (EAF) route, is ladle refined, vacuum degassed, continuous cast and rolled. These primary equipments are supplemented by best in class quality enhancing devices such as an automatic mould level controller, non-sinusoidal tundish oscillators, electro-magnetic stirrers etc., with the singular objective of producing the best steel
Carefully Chosen Inputs
The quality of inputs used for melting has a direct bearing on the quality of the output. For this reason, we melt a very carefully chosen mix of virgin metal (pig iron and DRI) and clean scrap so as to control the appearance of tramp elements. We have a trusted set of suppliers all of whom are periodically audited to ensure adherence to our standards. In addition, we test all incoming material for radiation and other hazardous contaminants
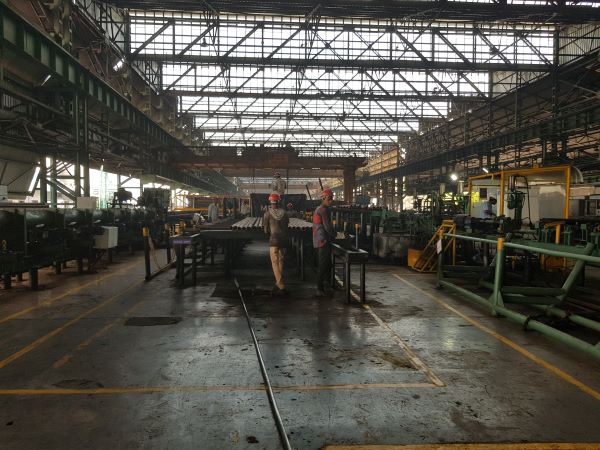
Clean Steel Process
ISMT prides itself on manufacturing the cleanest steel in the country, on par with the best worldwide this is entirely attributable to our steel making practices. While good equipment is a prerequisite for making Clean Steel, at ISMT, we believe that good practices are even more vital. While modern equipment may be procured at a cost, good practices are much more difficult to develop, and institutionalize it takes determination, time and painstaking effort. For this reason, throughout our 15 years of steel making history, we have focused on developing process knowhow, training people, and creating a committed quality culture. We are proud to say that our processes and practices are second to none. We follow a strict de-oxidation practice to ensure that macro inclusions of Alumina and Silica are floated out quickly from the molten metal. We ensure that the slag in the LRF is synthesized quickly and that the slag volume and chemistry are appropriate for complete slag killing. Similarly, low re-oxidation at the caster is ensured by controlling the superheat, achieving free opening consistently, and by adhering to proper tundish and mould practice.
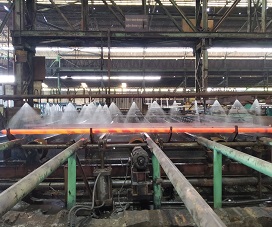
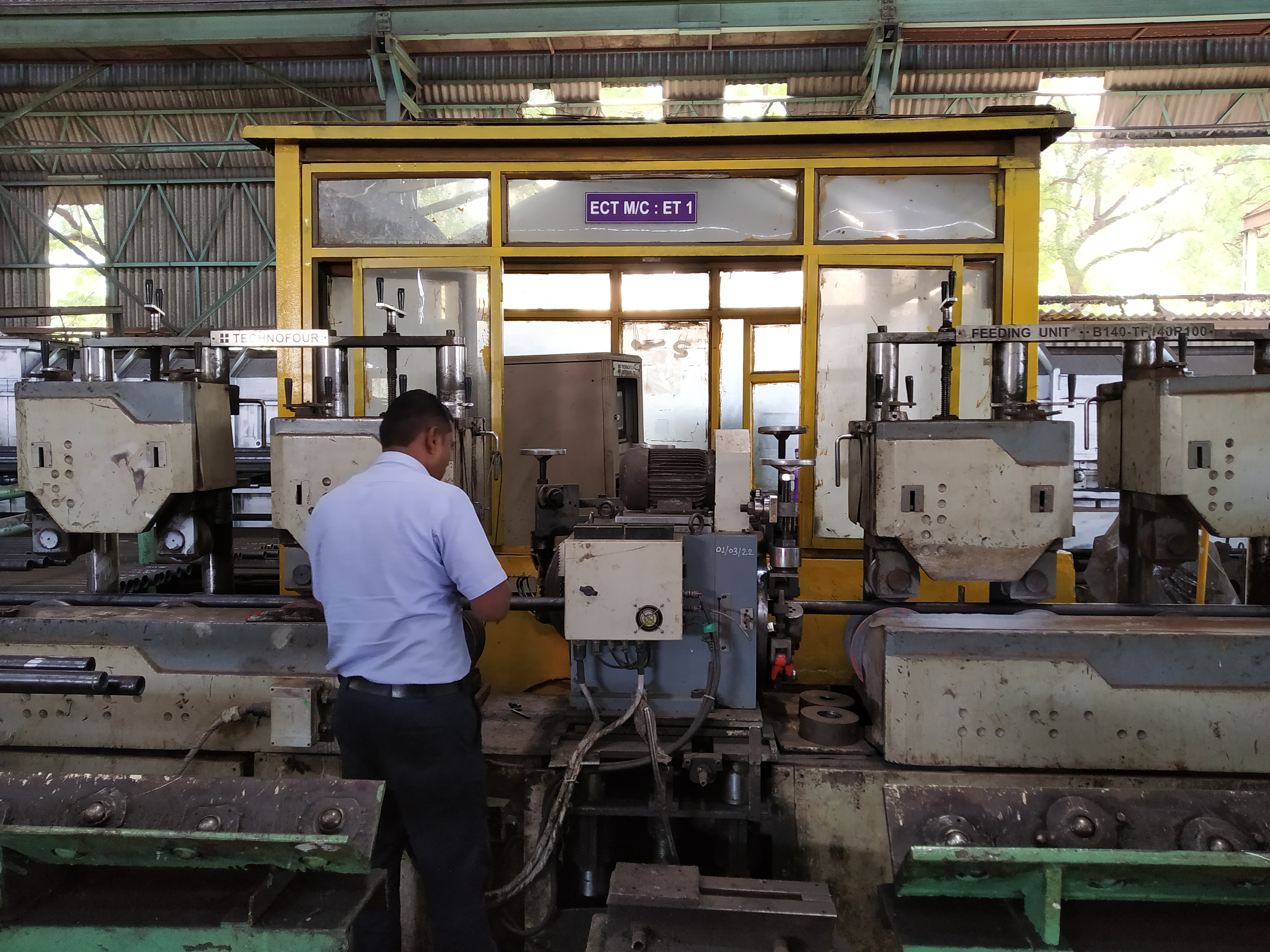
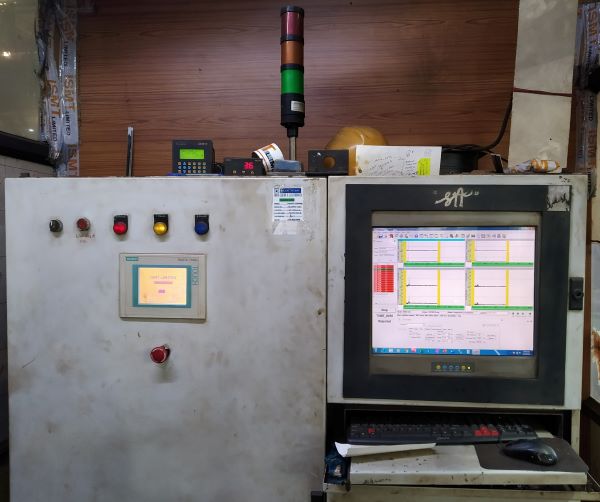
Application Based Steel Making
At ISMT, we like to understand where our steel is used. Where possible, our Technology Process Group (TPG) interacts with customers at the shop floor and at the R&D level to translate the customer's product requirement into a steel specification and a steel making process specification. This "Application Based" approach enables to deliver the most suitable and cost effective product. Today, given our history and our approach, we have developed an understanding of hundreds of applications that use our steels and we can use that experience to help you either select a steel or to develop a new grade appropriate to your requirements.
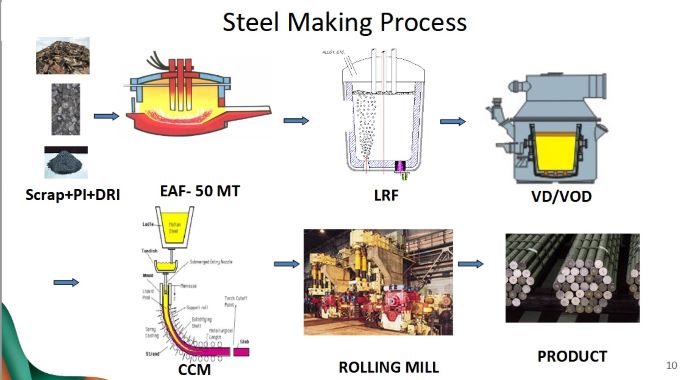
PROCESS FLOW | FACILITY | MAJOR ACTIVITIES/ PROCESS CONTROL CHECK POINTS |
||||||||||||||||||||||||||||||||||||||||||||||||||||||||||||||||||||||||||||||||||||||||||||||||||||||||||||||||||||||||||||||||||||||||||||||||||||||||||||||||||||
|
|
|
Installed Capacity | 350000 MT/annum |
Process Route | EAF - LRF - VD - CCM - RM |
Heat size | 45 MT |
Products | As Cast Rounds Rolled Round Corned Square (RCS) Bright Bars (Peeled / Turned) Cold Drawn / Cold Finished) |
Size Range As Cast Rounds Rolled Rounds Round Corned Square(RCS) |
160,180,200 And 225 mm dia. 25.4 to 115 mm dia for all application 125 to 170 mm dia for seamless tube industry 45 to 75 mm and 125 mm |
Standard Hot Rolled Sizes Rounds RCS |
25.4,26,26.4,27,28.3,30,32,34,36,38,40,42,45,48,50,52, 56,60,63,65,70,75,80,85,90,95,,100,105,115,125,137,150, 170MM AND AS CAST - 160,180,200& 225MM 45,50,52,55,60,63,65,70,75 MM AND 125 MM Additional size/ shapes upon specific request/agreement. |
Supply Lengths | Standard 3 to 6 m with 10% shorts down to 1 m or user defined. |
Straightness Tolerance Hot Rolled Hot Rolled and Machine Straightened Cast Product |
3.0 mm per meter 1.5 mm per meter 5.0 mm per meter |
Length Tolerance for fixed Length Supply | + 50, -0.00mm |
Condition of Ends | Standard Gas Cut / Hot Sheared (as per customer requirements) |
Standard Size Tolerance for Hot Rolled Bars / Billets |
|
Grades (lllustrative) | |
Plain Carbon Steels | SAE 1008,SAE 1010, SAE 1012, SAE 1019, SAE 1026, SAE 1035, SAE 1035, SAE 1040, SAE 1045, SAE 1518, 070M20, 080M40, 080M46, 070M55, CK35, CK45, CK55, CK60 etc.., and equivalent. |
Case Hardening Steels | 665M23, 635M15, 637M17, 815M17, 820M17, 822M17, SAE8617, SAE8620, 15Cr3, 16MiCr5, 20MnCr5, 15CrNi6, SCM415, SCM420, SCM421 etc., and equivalent. |
Spring Steels | 55Si7, 60Si7, 37MnSi5, 50CrV4, 38xc, 50Cr4V2, 51CrMov4, 52Cr4Mo2v etc.,and equivalent. |
Free Cutting Steels | SAE 1117,SAE 1137, SAE 1140, SAE 1141, 216M36, SAE 1144, EN-8M, EN-1A etc., and equivalent. |
Ball Bearing Steels | SAE 52100, 103Cr2, 100Cr6, SUJ2 etc., and equivalent. |
Micro Alloyed Steels | HMnV, 38MnSiVS5, 49MnVS3, C7056 etc., and equivalent. |
Other Alloy Steels | SAE 4130, SAE 4135, SAE 4140, SAE 4340, 817M40, 34Cr4, 37Cr4, 41Cr4, 25CrMo4, 42CrMo4, 40NiCrMo4, 40NiCrMo15, SCM435, SCM435, SCM440, SA182-F11, SA 182-F12, SA 181F11, T-5, T-9, T-23, T-91 etc., and equivalent. |
Ferritic Stainless Steels | AISI-410, AISI-420 |
Tool Steels | H-11 and H-13 |
Control Chemistry | Tramp Elements(max.) | ||
Carbon | 03 points | Tin | 0.02% |
Manganese | 05 points | Copper | 0.15% |
Sulphur | 10 points | Nickel | 0.20% |
Chromium | 05 points | Molybdenum | 0.05% |
Molybdenum | 05 points | Boron | 4 ppm max |
Grain Size Guarantee | ASTM 5 to 8 | Alternative grain size upon specific request / agreement. |
Inclusion Rating Guarantee | ||
Carbon & Alloy Steels | Thin series ABCD - 2max. Thick series ABCD - 1,5 max or as per cusotmer requirements. | |
SAE 52100 | Thin and Thick series A - 1.0 max., B - 0.5 max., c - nil, D - 0.5 max. | |
Resulphurised Steels | Thin and Thick series A - 3.0 max., BCD - 2.0 max. | |
Alternative inclusion rating upon specification request / agreement. |
Oxygen Level | ||
Carbon Alloy Steels | 25 ppm max. | |
Bearing Steels | 15 ppm max. | |
Alternative Oxygen level upon specification request / agreement. |
Hydrogen Level | 2 ppm max. |
Nitrogen Level | 80 ppm max. |
Titanium Level | 30 ppm max. in Ball Bearing Steel. |
Calcium Level | 10 ppm max. in Ball Bearing Steel. |
NDT Facilities | Ultrasonic testing, Spark, Spectral, Mobile spectrometer, MPL testing | |
Finish Supply Condition | As Rolled | Bright Bars |
Annealed | Drawn | |
Normalised | Peeled | |
Spheroidised Anealed | Ground | |
Quench & Tempered |